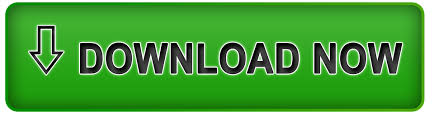
Sintavia recently used the new solidThinking Design Suite to optimise a traditional aerospace part. One such user is Sintavia, a global leader in independent metal additive manufacturing (AM) for critical industries such as aerospace, oil and gas, automotive and powder generation. In addition to these new features, all images rendered in Evolve will now include a Depth Channel (tiff), which can be used in post-processing tools including Adobe Photoshop to simulate natural blurring of foreground and background elements when viewed through a camera lens.īracket set up with loads and design space in Inspire.Įach of these enhancements has been implemented to streamline the overall design process by putting generative design and optimisation features into the hands of engineers and industrial users. Over in Evolve 2017, the biggest improvements come in the form of Planar Symmetry and Radial Symmetry tools to replace Mirror and Polar Copy tools.
SOLIDTHINKING INSPIRE BUY SOFTWARE
The updates to the software allow users to divide a part into a design or a non-design region by selecting a hole, pocket or face to offset. Topography Optimisation tools change the shape of shell structures using stamped bead patterns to improve structural performance. New users requested features for motion analysis, topography optimisation, symmetry and depth of field.īuilt to focus on improving usability for designers and engineers, key updates to Inspire 2017 include a new Motion tool that allows users to easily mechanise their models and predict loads for moving parts. These configurations can then be used to evaluate various design scenarios and the resulting concepts.SolidThinking has delivered the latest editions of its complementary design software products – solidThinking Evolve and solidThinking Inspire 2017. Multiple assembly configurations can be created. Users can decide which features are important and then pick the concept design best suited to their needs. Custom materials can also be added.Įxplore optimized shapes using a simple slider to add or remove material. Investigate linear static and normal modes analysis on a model and visualize displacement, factor of safety, percent of yield, tension and compression, von Mises stress, and major principal stress.Īltair Inspire is packaged with a material library including various aluminum, steel, magnesium, and titanium alloys. By utilizing Altair Inspire in the concept design phase, users can arrive at an ideal design concept extremely early in the process and reduce, or even eliminate re-design iterations.Ĭreate, modify, and de-feature solid models using Altair Inspire's modeling tools.Īltair Inspire offers a number of topology options including: optimization objectives, stress and displacement constraints, acceleration, gravity, and temperature loading conditions Inspire helps them to streamline the production of high-performance, quality parts and products. Simulation-driven design equips its users with the tools necessary to accelerate their overall design process. Leveraging simulation-driven design with Inspire early and often in the design process enables costs savings by reducing material usage, re-design iterations, and overall design time. This enables users to ensure a quality and dependable design prior to any prototyping or production.
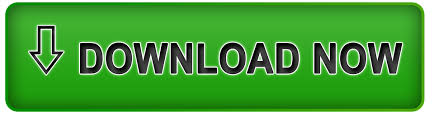